Photos: Jason Richards/Oak Ridge National Laboratory
In 2014, at the International Technology and Manufacturing Show in Chicago, a car was printed on the showroom floor. A massive 7'x13'x3' 3D printer—a collaboration between Oak Ridge National Laboratory, Local Motors, and Cincinnati Inc.—laid out a line of carbon fiber-infused plastic for 40 hours, building the body layer by layer.
That same year, Phillip Enquist, a partner in urban design and planning at Skidmore, Owings & Merrill, found himself at the University of Tennessee as part of a collaboration with ORNL. (The city of Oak Ridge was itself designed by SOM in 1942 as part of the Manhattan Project.) Oak Ridge had BAAM, the Big Area Additive Machine that had built the car (by 2015 it would build Bertha, a larger machine that could print 100 pounds an hour). Now it had an architect and designer on hand. So how do you top 3D-printing a car?
By 3D-printing a building.
"We cooked up this idea," says Brian Douglas Lee, another partner at SOM. “Could you actually generate a car that, through its engine and batteries, powers a house? And could the house also have a reciprocal relationship and power a car? That seemed reasonable. You could get solar collectors and power a battery; there's lots of people doing home batteries, like Tesla [the Powerwall], lots of cars that have battery resources, and with bidirectional charging, the house could power the car, or the car could actually help power the house."
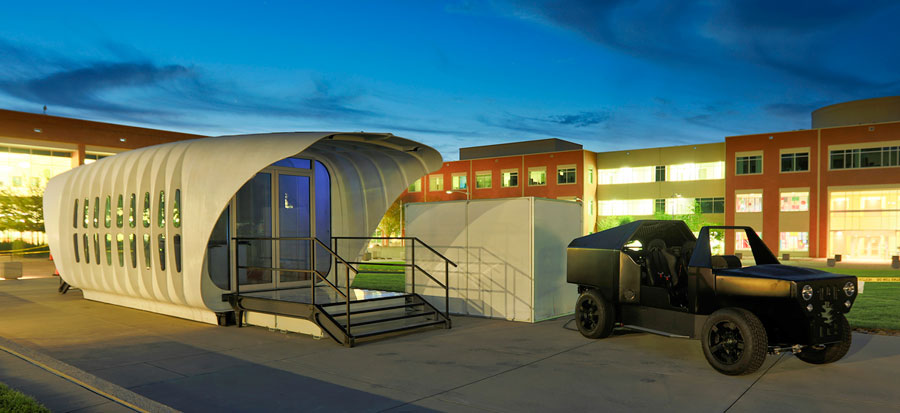
The result is the Additive Manufacturing Integrated Energy (AMIE) Manufacturing Demonstration project. The car (a PUV, or printed utility vehicle) is something of a homage to the old World War II Jeep Willys, themselves an early experiment in accelerated manufacturing. It connects through a wireless charging pad to the "house"—with a Murphy bed and kitchenette—which looks like something that pairs with a car: an Apple store meets an Airstream trailer. "It started out as being something that could travel," Lee says. "Some of the early designs started out looking like shipping containers."
Small, modular housing is not new, of course. Shipping containers themselves are actually en vogue as one form of it, and one of the project's partners was Clayton Homes, which makes mobile and prefab homes. But the pictures of AMIE don't really capture the material. It feels a bit like the plastic wood you find in benches and playgrounds, but it's heavy. (And as a plastic, it can also be recycled.)
"It's a little bit heavier than wood but five times as strong with the carbon-fiber-infused material," says Andrew Obendorf, an SOM associate director. "It's like a very fine plastic corduroy. If you had corduroy pants made of plastic, that's kind of what it looks and feels like. That's the process of laying down beads of material creates that texture."
But the structure of the building is relatively thin. Which is another part of the experiment.
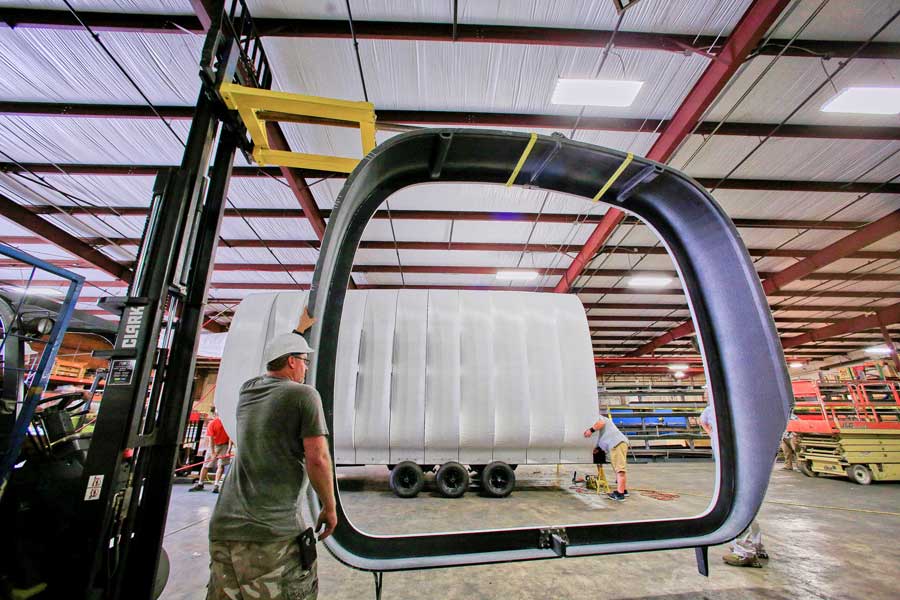
"At Oak Ridge, they had lots of people doing lots of different things—building enclosures, refrigerators, mechanical equipment. Insulation is one of the things they're very interested in, because you know how badly some houses are insulated," Lee says. "It's all about insulation, creating as tight an envelope as possible, so when you generate energy, you can use it within. Dealing with that super-insulation, that's not that thick or high-cost, it was one of the ideas that was a beginning influence on the project."
And in 2014, Oak Ridge was also working on a Department of Energy project about vacuum-insulation panels, which are thin but much more efficient than foam or fiberglass. It's like insulating a house inside a travel mug instead of inside a sweater.
Advertisement
"It's a piece of insulative material that's about an inch thick when they make it," Obendorf says. "That inch of material has an insulation property of about 40 on an R-value scale. That's about double what you get in your six inches of insulation that you have in your house. It's very high-value insulation. But the negative side of it is that it's vacuum-sealed. The vacuum's what gives it these properties. It's a material that's used a lot in refrigerators—places where you want to keep things very cold but you have a protected shell that it sits inside of."
The stiff 3D-printed plastic gave them a shell in which to place the effective but fragile vacuum panels. "That's where the printing came into play—we could print, essentially, around this panel that needed to be protected, couldn't be punctured," Obendorf says. "If it's punctured it loses almost all of its value."
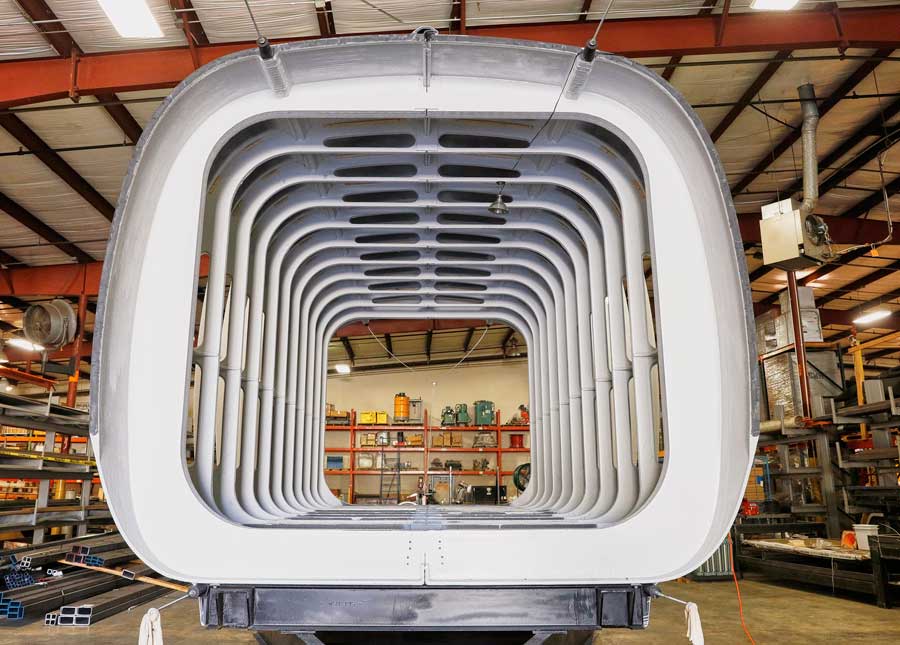
"You think about the way you deploy material differently," Lee says. "There's no waste; the whole thing's recyclable. You can then think about forms that are different than normally you might do. In design, it's always easier to make rectilinear things. Here you can come up with forms that are more organic, and more connected to the ways that they're actually stressed or fit together. That's why the thing is shaped the way it's shaped. It's really trying to take advantage of those properties of minimizing stress at the corners. Taking advantage of the fact that you can bend material out in a morphing way, so you get the light gills on the surface. To have a cantilever, a very thin material, for the canopy that stretches out."
Advertisement
But what's it for? For now, AMIE is mostly about exploring the concept and the technology.
"People have talked about a lot of different things—dormitories, the homeless, the military," Lee says. "But stepping back, though, for us it was a little more that, if you had to print a small structure and you want to explore this issue of 3D printing as a material, could you actually do a self-contained unit? It was about the technology of 3D printing first. If we wanted to really get serious about the applications of this in the next phase—in fact, we are—how can you actually create modular components that could even be smaller, or bigger, and be combinable to create structures that would serve lots of the needs that we see in society today?"
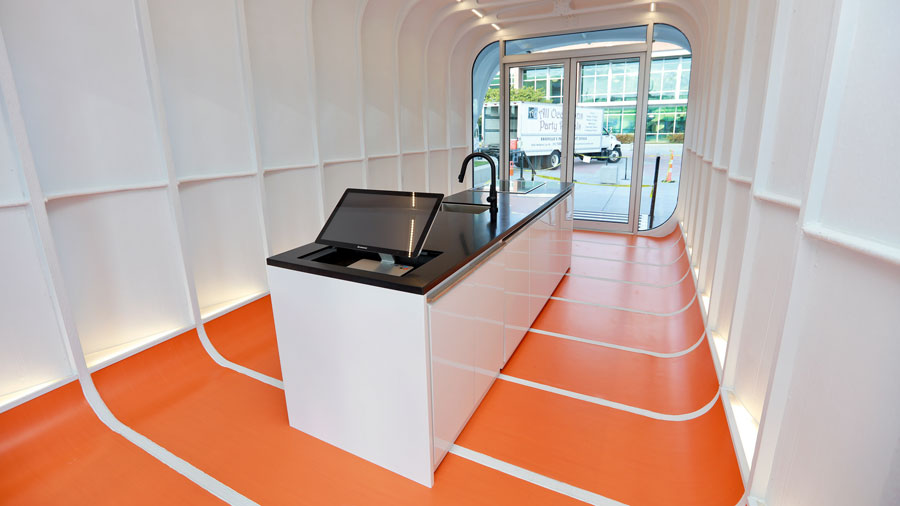